AUTOMOTIVE
In the automotive industry, electron beam welding has many applications; from turbochargers to gears and convertors, to shunt resistors in standard fuel, hybrid, and electric vehicles.
Electron Beam Welding of Turbochargers
Most modern passenger and commercial diesel vehicle engines have a turbocharger fitted, which means there are currently millions of vehicles benefiting from better fuel economy, performance, and lower emissions across the world.
At the heart of the turbocharger is the high-speed rotating impeller shaft assembly. Driven by exhaust gasses, the shaft forces fuel and air back into the engine.
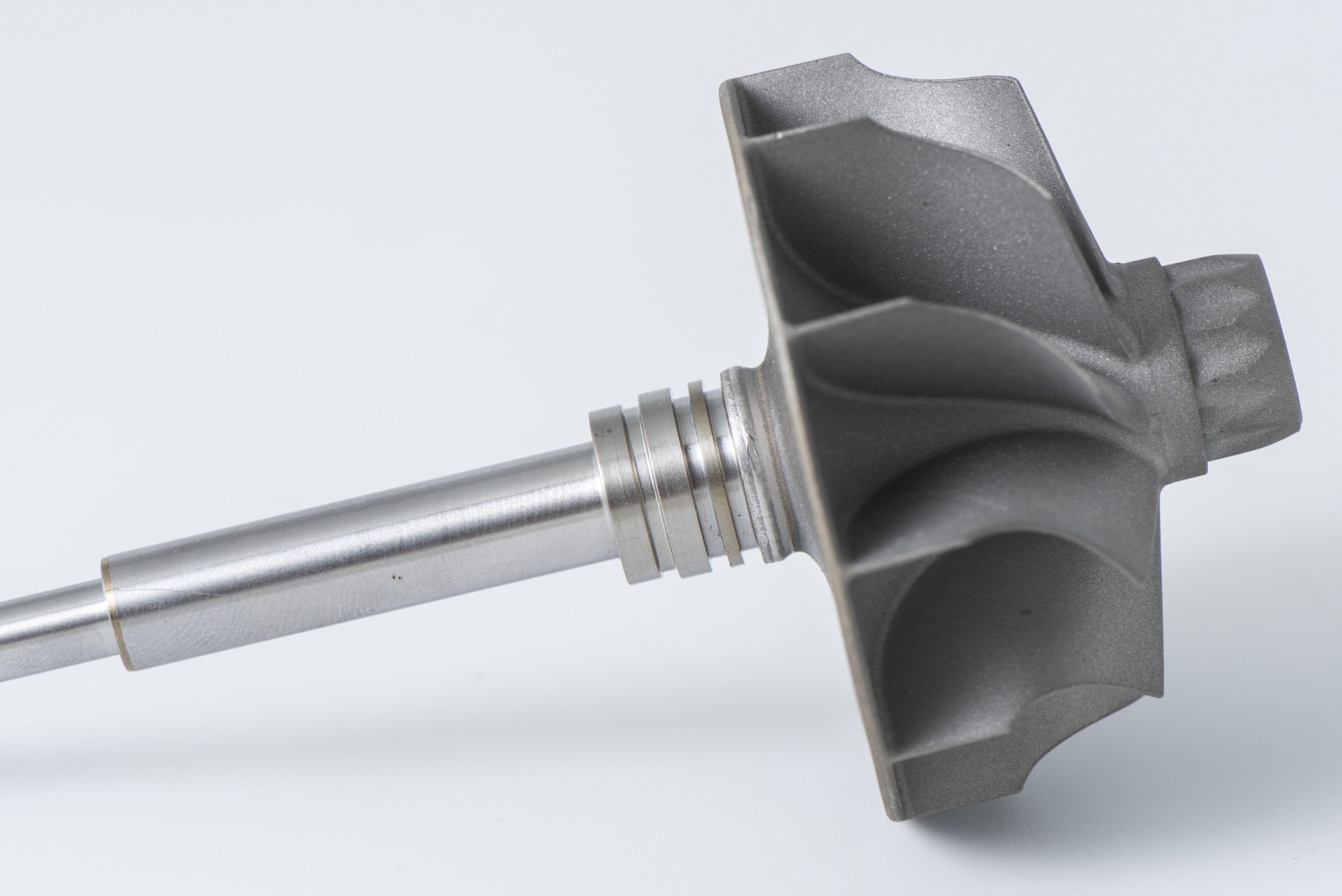
Electron beam welding joins a cast Inconel wheel and a carbon steel shaft together. The electron beam is a finely focused stream of electrons, which melts the two metal surfaces together, resulting in an excellent quality of weld with the characteristics of deep penetration, narrow fusion zone (HAZ) and near parent metal strength. Welding inside a vacuum environment ensures a clean and pure process.
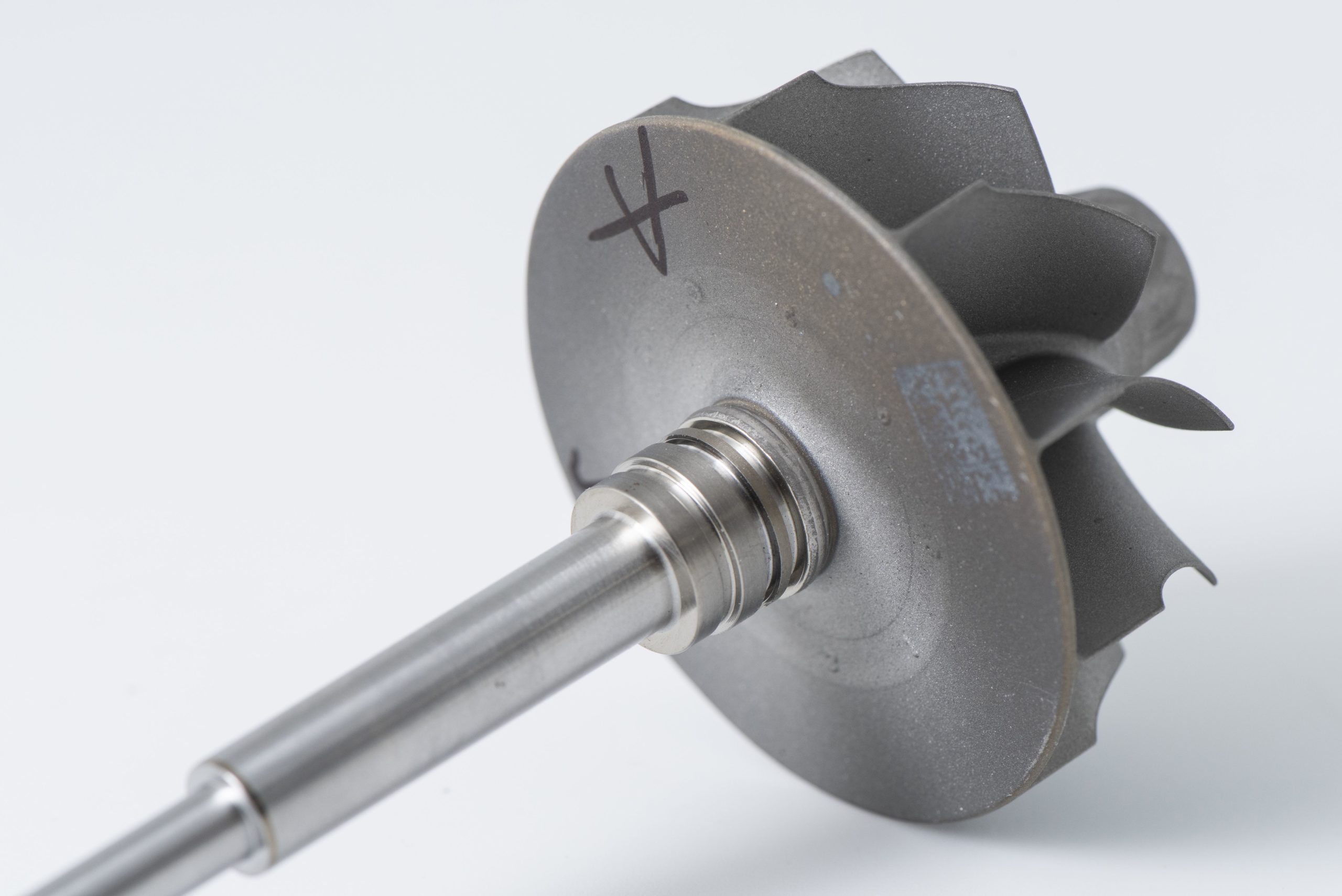
Parts are either machined with a spigot to make the joint self-locating or are butted together before welding and held with precision clamping to control the geometry. Parts can be welded in the finished or semi-finished condition to minimise post-weld machining and with the correct alignment of the beam at the rotor/shaft joint, accurate and repeatable welds are possible with no associated cracking.
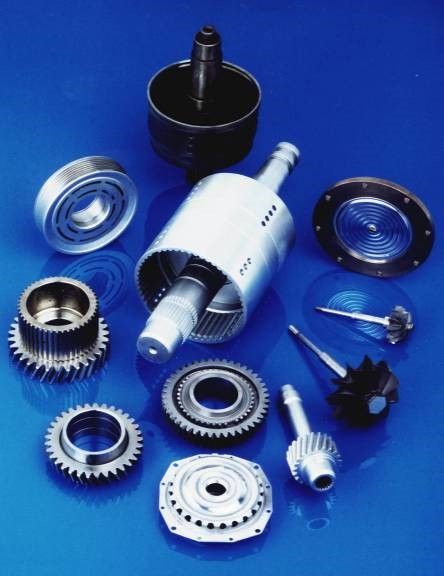